Electric vehicles are driving the SiC power semiconductor market, but cost remains an issue.
With the growth of electric vehicles as well as other systems, the silicon carbide (SiC) power semiconductor market is experiencing a sudden surge in demand.
But the demand has also led to a tight supply of SIC-based devices in the market, prompting some suppliers to increase fab capacity during the tricky transition to wafer size. Some SiC device manufacturers are transitioning from 4-inch wafers to 6-inch wafers.
SiC is a composite semiconductor material based on silicon and carbon. In the production process, specialized SiC substrates are developed and then processed in fabs to produce SiC based power semiconductors. Many SiC based power semiconductors and competing technologies are specialized transistors that can switch the current of a device at high voltages. They are used in the field of power electronics to enable the conversion and control of electricity in a system.
SiC stands out for its wide band gap technology. Compared to traditional silicon-based devices, SiC has 10 times the breakdown field strength and 3 times the thermal conductivity, making it ideal for high-voltage applications such as power supplies, solar inverters, trains and wind turbines. SiC is also used in the manufacture of leds.
The biggest growth opportunities are in the automotive sector, especially electric vehicles. SiC based power semiconductors are used in on-board charging devices for electric vehicles, and this technology is making its way into a key part of the system – traction inverters. The traction inverter provides traction to the electric motor to propel the vehicle forward.
For this application, Tesla uses SiC power devices in some models, while other electric vehicle manufacturers are evaluating the technology. Hong Lin, Analyst at Yole Developpement, said: “When people talk about SiC power devices, the automotive market is definitely the focus. The SiC activities of pioneers such as Toyota and Tesla have brought a lot of excitement and buzz to the market. SiC MOSFETs have potential in the automotive market. But there are still challenges, such as cost, long-term reliability and module design.”
Driven by automotive and other markets, the SiC power devices business reached $302 million in 2017, up 22% from $248 million in 2016, according to Yole. “Driven by the automotive industry, we expect a leap forward in 2018 due to the growth of Tesla Model 3 capacity with SiC MOSFET modules,” Lin said.
According to Yole, the SiC power semiconductor market is expected to reach $1.5 billion by 2023. Suppliers of SiC devices include Fuji, Infineon, Littelfuse, Mitsubishi, ON Semiconductor, ST, Rohm, Toshiba and Wolfspeed. Wolfspeed is part of Cree. X-Fab is the sole contract manufacturer for SiC.
Manufacture SiC
Power electronics technology plays a key role in the global power infrastructure. This technology is used in industry (motor drive), transportation (cars, trains), computing (power supply) and renewable energy (solar, wind). Power electronics technology enables the conversion of alternating current and direct current (AC&DC) in the system.
For these applications, the industry uses a variety of power semiconductors. Some power semiconductors are specialized transistors that act as switches in the system. They allow power to flow in the “on” state and stop in the “off” state.
Power semiconductors are manufactured at mature nodes. These devices are designed to increase efficiency and minimize energy loss in the system. Typically, they are rated according to voltage and other specifications, rather than according to process dimensions.
For many years, the dominant power semiconductor technologies have been (and still are) silicon-based, namely power MOSFETs and insulated-gate bipolar transistors (IGBTs). Power MOSFETs are considered the cheapest and most popular devices used in adapters, power supplies, and other products. They are used in applications up to 900 volts.
In traditional MOSFET devices, the source and drain are located at the top of the device. In contrast, power MOSFETs have a vertical structure where the source and drain are located on opposite sides of the device. The vertical structure enables the device to handle higher voltages.
The most important mid-power semiconductor device is the IGBT, which combines the characteristics of a MOSFET and a bipolar transistor. Igbts are used for applications ranging from 400 volts to 10 kV.
The problem is that power MOSFETs and IGBTs are reaching their theoretical limits and there is unnecessary energy loss. Device energy loss due to conduction and switching. Conduction loss is caused by resistance in the device, while switching loss occurs during the switching state.
Guy Moxey, Senior Director of power Marketing and Applications at Wolfspeed, said: “From 5 volts to several hundred volts, silicon MOSFETs have always been a great technology. When the voltage reaches 600 to 900 volts, the silicon MOSFETs are fine, but it starts to lose energy. Igbts are good lifters, but they’re not fast or efficient.”
This is where SiC comes in. Power semiconductors based on gallium nitride (GaN) are also emerging. GaN and SiC are both wide-band gap technologies. Silicon has a band gap of 1.1 eV. In comparison, SiC has a band gap of 3.3 eV and GaN has a band gap of 3.4 eV.
Mouser Electronics said in a blog post: “The electronic band gap is the energy gap between the top of the valence band and the bottom of the conduction band in a solid material. It is this band gap that enables semiconductors to switch current on and off as needed to achieve specific electrical functions.”
Wide-band gap devices have several advantages. For example, electric vehicles are driven by electric motor drivers, which traditionally use power MOSFETs or IGBTs. Wolfspeed’s Moxey said: “If you replace the original motor drive with SiC, then your drive loss will be reduced by 80%. This means you can use a smaller battery for the same range. Smaller batteries mean lower costs.”
At the same time, SiC based power semiconductors are used in 600 V to 10 kV applications. Moxey said: “600 to 1700 volts is suitable for most SiC applications. When the voltage reaches 3.3~10 kV, it is very suitable. Such as wind power and small grids.”
In the field of power supplies, GaN is used for applications ranging from 30 to 600 volts. “GaN and SiC are complementary technologies, not competing technologies,” Moxey said.
GaN and SiC devices are both faster than silicon, but also more expensive. “Currently, the cost per ampere of SiC MOSFET devices is more than five times higher than that of comparable IGBTs,” said Elena Barbarini, head of equipment at Yole’s System Plus Consulting unit.
In 2002, with the introduction of SiC diodes, the first SiC based devices appeared, followed by the introduction of SIC power MOSFETs in 2011. Similar to power MOSFETs, SIC-based devices are vertical structures.
SiC power MOSFET is a power switching transistor based on SiC. “A diode is a device that conducts current in one direction and blocks it in the opposite direction,” explains Rohm application engineer Mitch Van Ochten.
In any case, SiC power semiconductors are growing. “Silicon plays an important role in power devices,” said Mike Rosa, director of Strategy and Technology marketing at Applied Materials. But when you talk about higher power and lighter weight, manufacturers are looking at materials like SiC.”
Sic-based devices are produced in fabs, and the industry continues to transition to wafer size. “SiC can be used in either 4 – or 6-inch wafers,” said Rosa. The entire industry is desperately chasing 8-inch wafers.”
In fact, Cree has already made the transition from 4-inch (100mm) wafers to 6-inch (150mm) wafers. Rohm and other companies are in transition. SiC on 200mm wafers will not appear for some time.
Typically, when migrating to a new wafer size, the number of bare chips on each wafer will increase by a factor of 2.2. Larger wafer sizes can reduce overall production costs.
In the digital CMOS space, chip makers transitioned from 4 inches to 6 inches a few years ago. Making the same transition for SiC sounds simple, but there are some challenges. “While mass production of SiC power devices on 150mm wafers has been proven for nearly five years, the availability and cost of high performance, low defect density SiC substrates at 150mm remain barriers to adoption,” said David Haynes, senior director of strategic marketing at Lam Research.
“That said, as the transition to 150mm volume production materializes, the associated cost savings will help drive commercial viability in a growing number of applications,” Haynes said. Another example is the roadmap for SiC MOSFET technology. Planar SiC MOSFETs have been proven in commercial applications for some time, but today there is a significant push to develop and commercialize SiC MOSFEts for grooved structures that offer significantly lower on-resistance compared to planar structures.”
At the same time, in fabs, SIC-based power devices typically follow the same process flow as silicon-based chips. But there are some differences, such as the development of SiC substrates.
For silicon-based chips, the first step in the process is to develop the original silicon wafer. To do this, the silicon seeds are heated in a crucible. The resulting body, called a silicon ingot, is drawn and cut into silicon wafers of 300mm and smaller sizes.
For SiC, however, the process is to heat the SiC bulk crystals into a crucible, and the resulting ingot is pulled out and cut into thin slices.
For years, SiC bulk crystals have been plagued by a defect called microtubules, which are micron-sized holes that run through the crystal. Peter Gammon, Associate professor at the University of Warwick, said: “Microtubule defects and other defects that would disrupt the operation of the device are now almost eliminated. Material suppliers now offer zero-microtubule products.”
Once a SiC wafer has been developed, the next step is to form a SiC substrate. When a bare wafer is inserted into a deposition system, a SiC epitaxial layer grows on the wafer to form a SiC substrate. The SiC substrate is then processed in a wafer fab and defects are detected using a detection system. SiC devices are prone to defects, especially as suppliers move to larger wafer sizes.
“SiC has a lot of flaws,” said Lena nicolades, vice president and general manager of KLA-Tencor’s LS-SWIFT division. For SiC, our detection system uses a shorter wavelength. It can find breaks in the substrate.”
SiC in electric vehicles
At the same time, the automotive industry is the fastest growing segment of the entire semiconductor industry. Walter Ng, Vice President of Business Development at UMC, said: “More and more customers are redefining their product portfolios to suit the iot and automotive markets. This year, our automotive-related revenue has grown significantly. We expect auto-related revenues to continue to grow for the foreseeable future.”
SiC is also seeing growth in the automotive sector, especially in electric vehicles. Electric vehicles, including pure electric vehicles and hybrid vehicles, account for about 1% of global vehicle sales today. Driven by China and other countries, the electric vehicle market will grow from 1.6 million units in 2018 to 2 million units in 2019, according to Frost&Sullivan. By 2025, the market is expected to reach 25 million units.
Lam’s Haynes said: “The adoption of electric and hybrid vehicles is definitely going to be a reality. Globally, however, the timing and adoption rates vary widely and are closely tied to government policies and consumer access to appropriately priced products and charging infrastructure. There is no doubt that the Chinese market is the main growth engine for electric vehicles.”
In electric vehicles, there are several areas of the system, such as entertainment systems, on-board chargers, traction inverters, etc. The traction inverter converts energy from the battery to the traction motor, which propels the vehicle forward.
SiC is making inroads into in-car chargers, DC-DC converters and traction inverters. The car charger charges the vehicle via the grid.
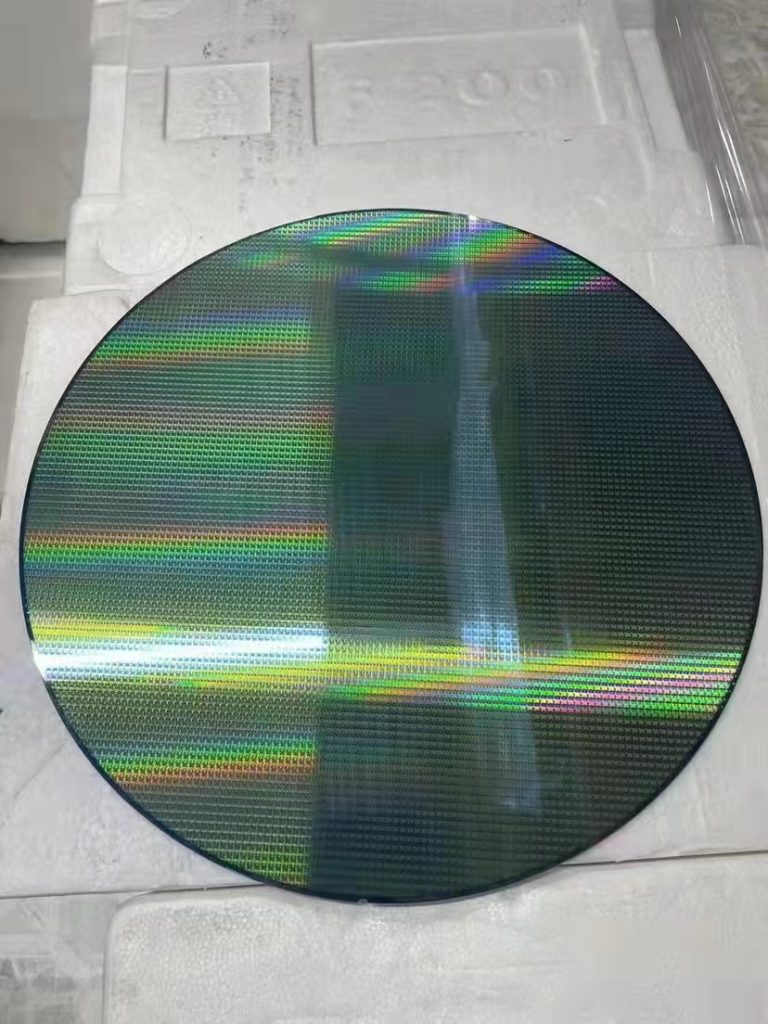
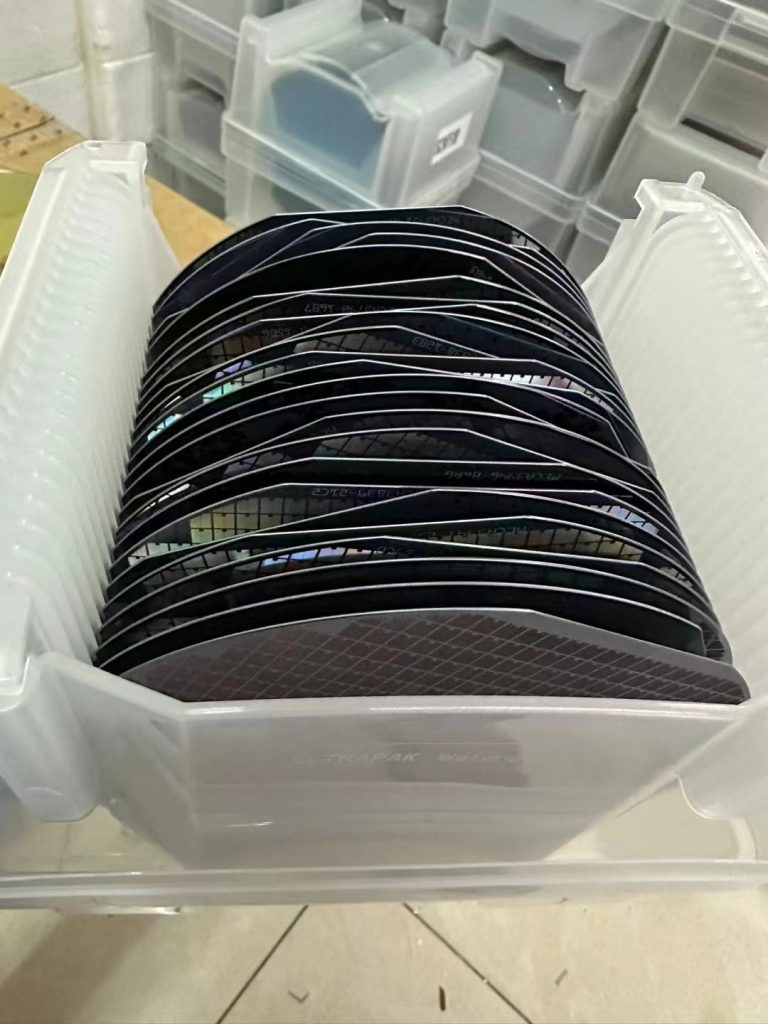
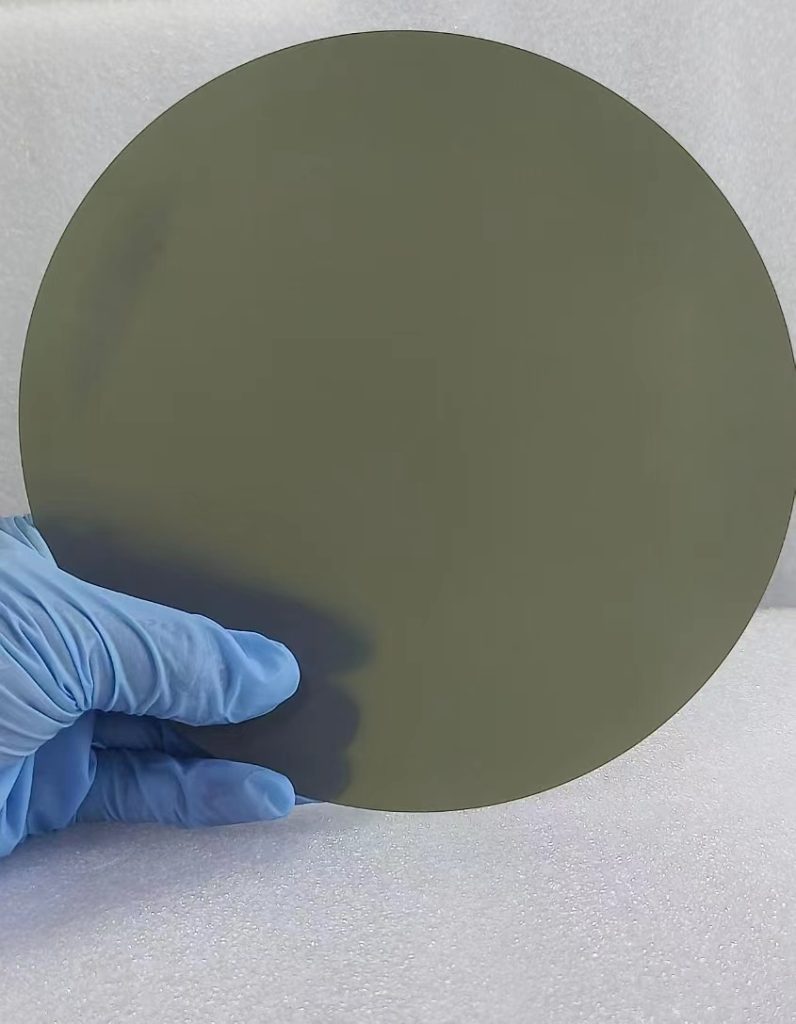
UNETRON SIC 4/6/8/12